News Story
Moldable Wood from Water ‘Shock’ Process
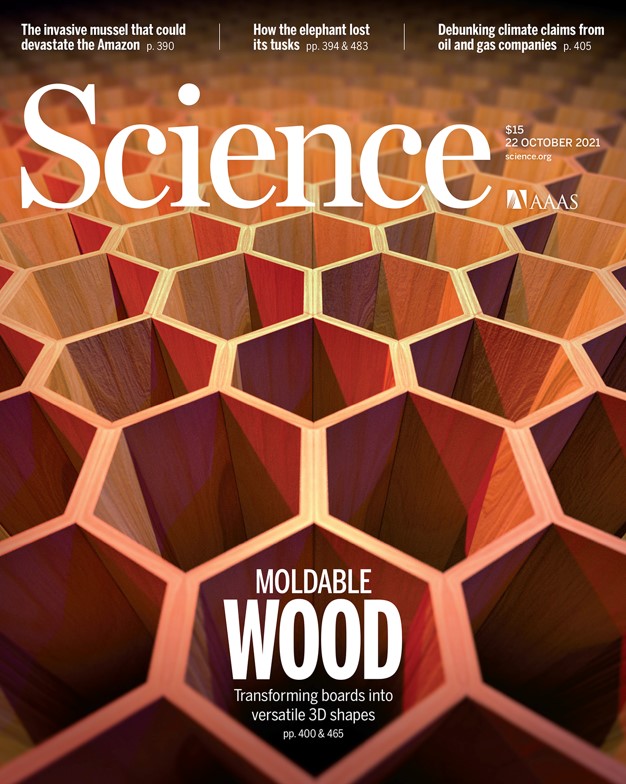
A wrinkling cell wall engineering strategy through partial delignification combined with a “water-shock” process to make wood stronger and moldable.
Structures and vehicles built with sustainable materials are an increasingly desirable asset these days, if we are to meet the needs of future generations. Natural wood already boasts an inherently lower life cycle cost than other materials and is a naturally strong, lightweight and durable material that could offer an attractive alternative to commonly used polymers and alloys, for example, if its properties and functionality could be improved. Various approaches, such as delignification and densification, have been tried and thus far failed to provide the same formability offered by metals and plastics.
To that end, a University of Maryland (UMD) research team led by Liangbing Hu, materials science and engineering professor and director of the Center for Materials Innovation, has developed a technique for creating strong and moldable wood materials via a rapid "water-shock" process.
After dismantling the wood’s lignin – the cell walls inside wood that give it strength – which softens it, and then closing the fibers via evaporation, the team re-swells the wood by "shocking" it with water.
"The rapid water-shock process forms a distinct partially open, wrinkled cell wall structure that provides space for compression as well as the ability to support high strain, allowing the material to be easily folded and molded," Hu said. "The resulting 3D-Molded Wood is six-times stronger than the starting wood and comparable to widely used lightweight materials like aluminum alloys."
This ‘moldable wood’ can then be folded into different shapes and then set to dry before forming the final product. The remarkable foldability of the processed wood originates in its wrinkled cell wall structure, which can sustain severe folding without fracture.
"Moldable wood significantly broadens the potential applications of wood as a sustainable structural material, while reducing the environmental impact for buildings and transportation applications" said Teng Li, mechanical engineering professor at UMD and co-author on the study.
Indeed, "this out-of-the-box approach to developing advanced wood materials will drive wood product and market innovation as a sustainable solution to replace many unsustainable structure materials and combat climate change," said JY Zhu at the USDA Forest Products Lab. "It will also facilitate mitigating forest thinning cost for healthy forest management to reduce wild catastrophic forest fires. We at the U.S. Forest Service Forest Products Laboratory are very excited to collaborate with Professor Hu on this research."
This study, which made the cover of Science on October 21 (DOI: 10.1126/science.abg9556), was a collaborative effort between the University of Maryland, Yale University, Ohio State University, USDA Forest Service, University of Bristol, University of North Texas, ETH Zurich, and the Center for Materials Innovation.
"The researchers introduce a clever means to transform the naturally occurring, straight-walled cellular structures of wood into wavy, accordion-like geometries, at the microscale," said John Rogers, professor of materials science and engineering, biomedical engineering and neurological surgery at Northwestern University. "The result is an unusual, high-strength form of wood that is both flexible and moldable, in ways that open up new applications for this very old class of material."
Dr. Hu founded InventWood LLC in 2016 to commercialize the advanced wood technologies invented at his lab, including this 3D moldable wood. For additional details, visit: www.inventwood.com.
For additional information:
Xiao, S. et al. (2021) Lightweight, Strong, Moldable Wood via Cell Wall Engineering as a Sustainable Structural Material, Science (Oct 21, 2021, Cover Story). DOI: 10.1126/science.abg9556.
Additional praise:
"The combination of making wood formable, while keeping its natural fiber structure is really a big achievement," said Peter Fratzl, professor of bioengineering and director at the Max Planck Institute of Colloids and Interfaces in Potsdam, Germany. "The result is a biobased material that preserves the strength of wood and gains the flexibility of plastics."
Stephen Eichhorn, a materials science and engineering professor at the University of Bristol recalls a childhood memory of his father building his own plane out of wood. "He bent the wood to be used in the wings of the plane using steam," Eichhorn said. “To see now that it is possible to make this flexible wood, while also enhancing the mechanical properties makes this a truly amazing material, and who knows – it could be used as a future material in aerospace!"
Published October 21, 2021