News Story
Turning Up the Heat
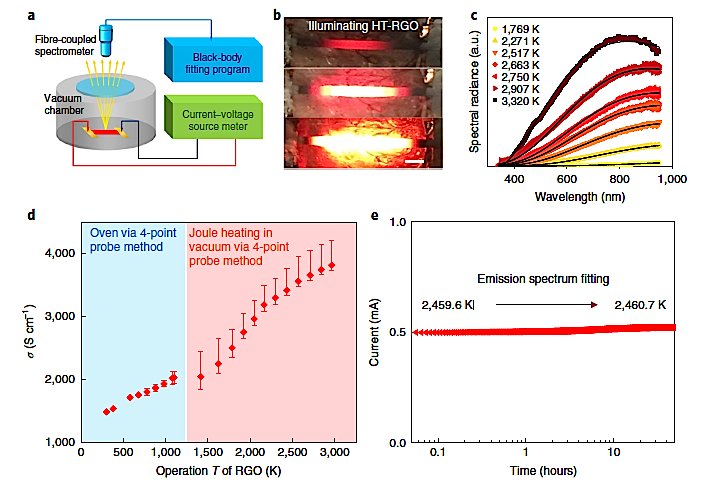
Image: High-temperature operation capabilities of HT-RG O films. a) Experimental set-up for in situ monitoring of incandescent radiation emission from free-standing HT-RGO films. A fibre-coupled spectrometer was used to analyse the emitted radiation. b) Photographs of a suspended, Joule-heated HTRGO film as its temperature reaches 3,300 K. The RGO strip emits more brightly over a greater fraction of its length as the input voltage increases. Scale bar, 1 mm. c) The measured emission spectrum taken from the centre of the ribbon, fitted to the Planck function and used to determine the temperature of each HT-RGO film. d) Electrical conductivity versus operation temperature for HT-RGO strips annealed at 3,300 K. e) A 3,300-K-treated RGO strip continuously emits over 50 h under a constant applied voltage of 6.30 V. A slight deviation in temperature over time of the emission spectrum is observed by the Planck fitting.
The United States consumes roughly 98 quadrillion Btu of total energy on an annual basis - most of which is used in transportation and industrial applications. According to the Lawrence Livermore Laboratory, over 66% of the total energy produced in 2016 was logged as “rejected energy,” most of which is heat. Since transport and industrial processing accounts for a great deal of energy consumption and heat loss, it makes sense to focus on recovering waste heat in these sectors and converting it into additional, usable energy.
In any heat engine – whether it be internal combustion (e.g., automobile) or external combustion (e.g., coal, natural gas or nuclear power plants) – waste heat is a byproduct that is either released into the air, or into a water source. Higher temperatures – above 1500K – are desirable because they promise a higher Carnot efficiency; that is, the maximum efficiency limit that any heat engine can obtain, depending exclusively on the difference between hot and cold temperatures. Until now, developing materials that can withstand such intense heat has been a challenge. Thermoelectric (TE) materials – such as bismuth telluride (Bi2Te3) and silicon germanium (SiGe) – have traditionally been used to generate electricity in heat engines. (To be efficient, TE materials must include both high electrical conductivity and low thermal conductivity – difficult criteria for a single material to hold – to ensure that when one side is heated up, the other side remains cool.) These materials, however, are rare on earth, thus, expensive to produce.
To solve these challenges, researchers at the University of Maryland (UMD) Department of Materials Science and Engineering (MSE) - led by Professor Liangbing Hu - have utilized nanostructures to develop a reduced graphene oxide (RGO) film capable of withstanding heat up to 3,000K. To put this in perspective – that’s more than double the temperature of the hottest volcano on record.
“The material is highly efficient, with a record high power factor of 670 µW/m·K2 among carbon-based materials,” said Tian Li, an MSE post-doc and first author on the corresponding research paper. “The RGO ribbon is non-toxic, lightweight, highly flexible – you can cut it into any shape you need – and attractive for system integration and scalable manufacturing. Currently, we can make each film about 1 inch by 1 inch.”
The graphene oxide film was first made via a solution based process, which was “then pre-reduced to RGO in a tube furnace under a H2/Ar (5%/95%) atmosphere at 1,000 K for one hour with a 5 oC min−1 ramp rate to ensure a uniform film before Joule heating,” the team stated in their paper. “The RGO film was subsequently treated at high temperature (2,000 K, 3,000 K and 3,300 K) by applying the required amount of electrical current through the film via Joule heating.”
The team has also developed innovative methods to characterize the electrical and thermal conductivity, as well as the Seebeck coefficient of the film up to 3000 K.
What’s more, this material can effectively absorb radiation and convert it, too, into electricity. “The HT-RGO can also facilitate broadband optical absorption with an extremely high absorption coefficient per layer,” said Li.
The remarkable TE performance of this RGO film makes it a promising material for a broad range of applications beyond concentrated solar power (CSP), including radiation energy conversion, TE topping cycles for power plants and direct energy generation from hydrocarbon combustion.
For additional information:
Li, Tian, et al., Hu, Liangbing, “Thermoelectric properties and performance of flexible reduced graphene oxide films up to 3000 K”. Nature Energy, 05Feb2018. DOI: 10.1038/s41560-018-00934.
Published February 12, 2018