News Story
"Mining" the Sea for Uranium
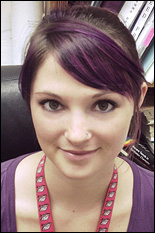
Nuclear engineering graduate student Chanel Tissot.
But don't worry about that trip to the beach or fish you had for dinner, she says. Uranium, like many other elements, is found naturally just about anywhere.
"It's all about concentration," she explains. "The uranium is so diluted in such a vast amount of seawater, it amounts to about 3 parts per billion. That's significantly lower than a uranium-rich part of the earth where you would mine for it."
Despite that very low concentration, collecting uranium from seawater is an attractive alternative to mining: It can be accomplished using a passive process that requires no pumping, electricity, digging or milling. It has virtually no environmental impact, leaves behind no toxic waste, and is far less hazardous for workers.
In a study conducted from 1999 to 2001, a team of Japanese scientists demonstrated that polyethylene fabric treated with a chemical known to bond with uranium ions could be used to filter or "soak up" uranium from seawater. The uranium ions would be released by exposing the fabric to an acid bath, and remain in a solution until they could be extracted and enriched for use as fuel.
Unfortunately the material could only be used once or twice before it needed to be replaced, and the process was not efficient enough to offset the cost. Since then, research groups around the world—including Tissot's, led by her advisor, Clark School Department of Materials Science and Engineering professor Mohamad Al-Sheikhly–have been vying to be the first to discover how to turn the concept into a commercial success.
Tissot, Al-Sheikhly and their colleagues may have the solution. Tissot says her team's novel combination of an ultra-high surface area fabric and a specific chemical have enabled them to extract 97 percent of the uranium from a sample of seawater. The chemical is bonded to the fabric using a process called radiation grafting, which keeps it from washing off when exposed to the water.
To date, they have tested the product in the laboratory using small fabric swatches. "Most of the work on this project is optimizing the materials: choosing what [fabric] you're going to use, what chemical you're going to use, the solvents, [radiation] dose rate, total dose, [and] type of radiation," says Tissot.
The team's next steps involve improving the durability of the fabric so it can be reused, reducing the amount of time it needs to remain in the water, and optimizing the production process so it can be scaled up for ocean trials and eventual commercial use. The team is also working on a version of the product designed to capture cesium, which can end up in water as a result of a nuclear accident, such as the one that occurred at the Fukushima Daiichi power plant following the 2011 earthquake and tsunami in Japan.
Tissot says the Clark School is an ideal place to work on the project, thanks to its advanced radiation facilities—facilities so good, she adds, that competing research groups come to use them.
Tissot has been invited to deliver her findings in a presentation titled "The Extraction of Uranium from Seawater Using Advanced Radiation-Grafted Materials" at the Tenth Meeting of the Ionizing Radiation and Polymers Symposium (IRaP) to be held in Cracow, Poland in October 2012. Her trip will be funded in part by an IRaP Student Grant Award.
The Al-Sheikhly Group conducts this research in collaboration with Professor Aaron Barkatt (Department of Chemistry, Catholic University of America) and Dr. Jay A. Laverne (Department of Physics, University of Notre Dame). Tissot's work is funded by a Nuclear Energy University Programs grant from the U.S. Department of Energy.
Published July 9, 2012